nachdem nun fast alles fertiggestellt ist, scheint es mir an der Zeit hierfür ein eigenes Thema auf zu machen.
Bin ja schon etwas länger (viel zuuuu lange

bzgl. Steuerung (bzw. Schaltvorgänge bei hoher Last - siehe hier http://forum.mosfetkiller.de/viewtopic.php?f=3&t=63392)
oder bzgl. Schweißzangenkonstruktion (s. hier: http://forum.mosfetkiller.de/viewtopic.php?f=3&t=63517)
oder hitzebeständige Sekundärwicklung (s. hier: http://forum.mosfetkiller.de/viewtopic.php?f=3&t=63496)
1. Trafoaufbau
Habe als Basis einen alten klassischen Schweißtrafo mit 5 Schaltstufen auf der Primärseite verwendet - Leistung ca. 3-4 kVA.
Die Sekundärwicklung habe ich entfernt und stattdessen 3 x 4 Windungen mit 35 mm2 + 1 mal 12 mm2 eingebracht (mehr ging nicht rein). Um die Hitzebeständigkeit der Sekundärwicklung zu steigern, habe ich die Gummiummantelung vom 35mm2 Kabel entfernt und durch Glasfasergewebe ersetzt das ich mit Hochtemperatursilikon um die nackte Kupferseele gewickelt habe. Dadurch hat sich der Durchmesser der einzelnen Stränge deutlich reduziert und die Temperaturbelastbarkeit dürfte bei ca. 300 Grad C liegen

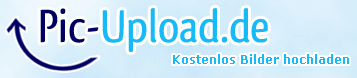
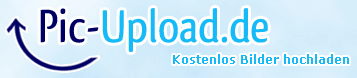
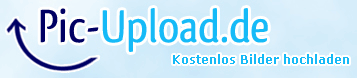
habe mir für das Bewickeln extra eine Haltevorrichtung bauen müssen, die das Kabel eng auf Spannung hält und dafür sorgt, das sich die geflochtenen Adern nicht entflechten.
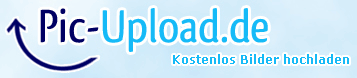
Und hier die fertige Sekundärseite (war gar nicht einfach, das doch recht sperrige Kabel hier eng und stramm aufzuwickeln und seitlich herauszufürhen:
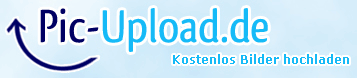
die Kabelschuhe sind selbstgemacht aus 10 + 12mm Kupferrohr und mit großer Crimpzange angecrimpt:
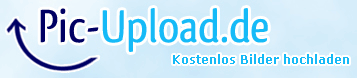
Da sich der Spulenkörper etwas auseinander gedrückt hatte, war es nicht einfach die Trafobleche wieder ordentlich hinein zu bekommen. Ich mußte etliche Schraubzwingen, etwas Gewalt, viel Gefühl und Geduld aufbringen:
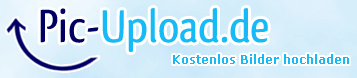
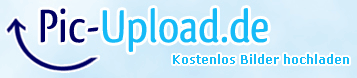
Am Ende passten die Trafobleche im Stoss nicht 100%ig aufeinander - es sind einige Lücken von ca. 1 mm geblieben - ich hoffe, das das der Leistungsübertragung nicht abträglich ist? Habe jetzt wohl einen Trafo mit kleinem Luftspalt - aber ein Schweißtrafo hat ja eh eine recht lockere Kopplung

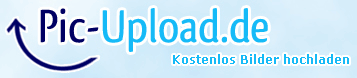
2. Steuerung der Schaltvorgänge / Einschaltstrombegrenzung
Das Thema wurde schon in dem oben erwähnten Thread ausführlich diskutiert. Habe mich letztendlich für 2 Solid state Relais (SSR) entschieden, eines mit 40 A und eines mit 60 A. Das kleinere schaltet über einen 12 Ohm Widerstand die Primärwicklung ein, der Widerstand begrenzt den Einschaltstrom auf max. 20 A. Nach ca. 400 ms schaltet der größere SSR durch und übbrückt diesen Widerstand, so dass dann der volle Strom fließen kann. Die 400 ms sorgen für eine gewisse Vormagnetisierung des Trafokerns (sofern diese bei kurzgeschlossener Sekundärwicklung beim Punktschweißen wirklich stattfindet - zumindest teilweise hoffentlich). Der Widerstand wurde aus 1mm Edelstahldraht selbst gewickelt (12 m auf Fliesenstreifen) - sollte ca. 1000 W aushalten und für 0,5 sec. auch locker 5 kW (tut er auch - wird ca. 100 - 200 Grad heiß). Die komplette Einschaltsteuerung wurde der Größe wegen in einem eigenen Gehäuse unter gebracht und wird per Fußschalter gesteuert. Dies hat auch den Vorteil, das man sie für andere Projekte und zum Testen großer Lasten verwenden kann

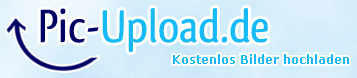
Und hier der Testaufbau (noch mit handgeführten Schweißelektroden bzw. eine im Schraubstock eingespannt):
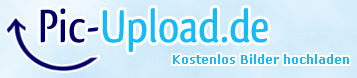
Die Verbindungskabel vom Trafoausgang zu den Elektroden ist über 150 mm2 Cu-Kabel mit entspr. Kabelschuhen hergestellt. Das Kabel hat einen Außen-DM von 18mm, reines Cu 14 mm:
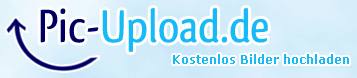
Es kommt sehr auf gute, widerstandsarme Kontakte an! Bei einem Kabelschuh waren die Schrauben nicht ganz fest angezogen, er wurde sehr schnell heiß! Ein festes Anziehen hat dies deutlich reduziert und damit kommt natürlich auch mehr Leistung am Werkstück an

Dennoch werden die Elektroden innerhalb von 2-3 sec. so heiß, dass man sie mit der bloßen Hand nicht mehr halten kann.
Und hier ein paar erste Probeschweißungen (1 und 1,5 mm Edelstahlblech - einfach von Hand gepunktet):
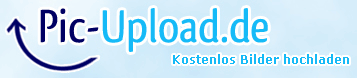
1mm hält bombig, 1,5 mm sind grenzwertig. Habe aber bisher max. Stufe 4 (von 5) genutzt und der richtige Pressdruck wird erst mit der richtigen Punktschweißzange erreicht. Diese ist noch in Konstruktion:
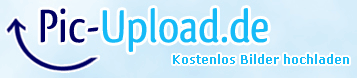
Aus 4 - 6 mm starkem Stahlblech geschweißt. (Das Schweißen muß ich noch üben, ist tlw. ein heilloses Gebrate mit Elektroden geworden). Naja, das Übelste habe ich mit der Flex und wieder Drüberbraten behoben...

Und das werden die Elektroden für die Zange (10 mm Cu-Rundmaterial, das dann in 20 x 8 mm Schienen eingespannt wird):
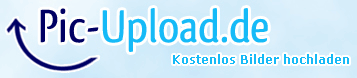
So 100%ig ist die letzte Konstruktion noch nicht ausgegoren. Arbeite parallel noch an einem Modell aus Holz

Ich habe auch mal einen Variac (10 A) vorgeschaltet um den Strom bei kleinerer Eingangsspannung messen zu können. Bei ca. 70 V primär fließt ein Kurzschlußstrom von ca. 700 A (bei massivem Kurzschluß über Cu-Schine 160mm2 direkt am Trafoausgang). Wenn ich das hoch rechne auf 240 V Netzspannung dürte man gut 2 - 2,5 kA erwarten können, natürlich nur bei guten Kontakten. Realistisch sind wohl 2 kA. Das sollte für 1 - 1,5 mm Edelstahlblech wohl reichen bei genügend Pressdruck.
Das schöne ist, die Schaltsteuerung hat es bisher anstandslos mitgemacht. Den vollen Primärstrom habe ich noch nicht gemessen, wird vermutlich um die 30 A liegen, kurzzeitig evtl. 40A. LSS ist C16, als 16 A träge - das hat bis jetzt gereicht

Alles in allem bin ich recht zufrieden - nur die Projektzeit war vieeel zu lang

Melde mich nochmal, wenn die Schweißzange fertig ist mit einigen Ergebnissen
